Success stories
QuAInS consistently provides industry-leading digitalized inspection and quality big data solutions to customers in various industries, helping them to improve quality management, reduce costs, and improve delivery rates, including but not limited to semiconductor, electronics, photovoltaic, photovoltaic, Machinery, precision parts, automotive, energy, chemical, electrical and many other industries.
The following content is in the confidentiality of customer information, and the customer name is specifically omitted.
Case 1: A precision machinery parts manufacturing company enhances quality control
Challenge: Company A is a well-known manufacturer of precision components. One of its businesses is to provide a variety of high-precision components to many of the world's top hard disk suppliers, including Western Digital (WD). Company A produces hundreds of thousands of parts every month. The customer's requirements for the quality indicators of the parts are very strict (three or more after the decimal point). The problems caused by this are:
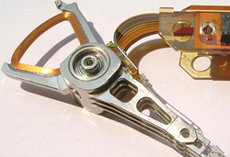
1. Due to the lack of real-time quality monitoring and early warning mechanisms, each time a quality problem is discovered, a large number of defective products have often been produced, which has caused a lot of waste of raw materials, and also caused a lot of rework and scrap , Resulting in high costs;
2. Many data produced by measuring instruments (such as coordinate measuring machines, micrometers, projectors, balances, rotational inertia measuring instruments, gravity and center of gravity measuring instruments, etc.) are manually recorded. This aspect leads many people to think that False data and erroneous data, on the other hand, it is difficult to analyze the data in time to find quality problems and formulate solutions in a timely manner, wasting precious data resources.
3. There are nearly 400 production equipments on the production line, and there are multiple fixtures on each equipment. When quality problems are found, it is impossible to locate in time and accurately which equipment or fixture may have potential quality problems, so as to compare Seriously affected the use of production capacity.
4. Since the company does not have an automatic quality monitoring and reporting system, on the one hand, it is necessary to arrange dedicated engineers to spend a lot of time to produce various quality reports (including quality evaluation, calculation process capabilities, etc.); Invisibility, customers often question the company's quality management, and the quality management department is under great pressure to cope with customer audits.
Solution: After repeated inspections and careful evaluations, Company A finally chose QuAInS for data acquisition and management and real-time quality monitoring (warning and reporting) as the first phase of the company's quality analysis and innovation system based on the actual situation of the company. .
Achievements: The QuAInS professional team completed the implementation of the system for Company A in three months, and provided professional training for the relevant measurement personnel and quality management personnel. After the system has been running for a while, it has achieved very good results:
- The number of scraps and rework due to quality problems has been greatly reduced, while the production capacity has been significantly increased while the unit quality cost has been significantly reduced.
- Able to carry out the maintenance and management of the measuring tools more effectively, maintaining a clear view of the maintenance records and status, and ensuring the accuracy of the measurement data
- When quality problems occur, the problem resolution cycle is shortened by nearly half, which becomes one of the important reasons for the increase in production capacity;
- The time required to prepare a quality report has been reduced by more than 40%. The pressure of quality management personnel on customer review has been greatly reduced, and customers are more satisfied with the company's quality management status.
Case 2: A well-known semiconductor company improved the level of quality analysis and product yield
Challenge: The company is a world-renowned manufacturer of storage media and solid-state hard drives. In the semiconductor and electronics industry, where the precision of production processes is generally high, the company's quality management level is already very good, and the quality management statistical methods have been used in the company. Widely used in the industry, the company not only purchased professional quality management statistical analysis software, but also equipped with a dedicated industrial statistics team.
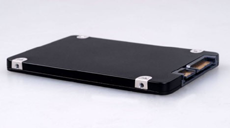
The company has three or four hundred engineers. " Of course we have professional statistical analysis software, but we cannot expect every engineer to become an industrial statistics expert," the company's quality manager mentioned. Experts from the industrial statistics team can help ordinary engineers develop relatively standardized analysis ideas and strategies based on the company's own actual situation, but "how to build a reliable platform for ordinary engineers to easily perform daily quality problem analysis through this platform, And the company must have good authority control over their accounts "has become one of the important challenges in quality management. In addition, traditional real-time SPC quality monitoring can only point out which equipment may have problems. The situation is that engineers often Tired of running between production equipment to analyze and solve problems one by one. Therefore, "how to easily find the commonality between common problems (common problem incentives) and improve the efficiency of problem solving" has also become an important challenge.
Solution: QuAInS developed a routine quality analysis automation system for engineers to use.
Achievement: The company's industrial statistician team has achieved a good way of interaction with ordinary engineers: the industrial statistics team provides analysis methods and ideas. Engineers only need to analyze according to the set number of analysis methods. They have more Time and effort to help companies improve their quality management level, training time and cost of industrial statistical methods and software are greatly reduced.
Case 3: A leading photovoltaic module and system supplier in an industry reduces scrap losses
Challenge: The company is the largest ground concentrating photovoltaic manufacturer in China, specializing in providing integrated solutions for ground concentrating photovoltaic modules and systems from design, research and development, production, sales, installation to service.
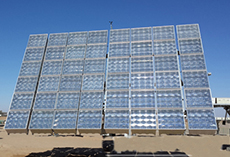
The company has more than 500 engineers. The level and ability of engineers and other skilled workers fluctuate greatly, and the turnover rate is high. Due to the high value of the core module of the product, sometimes the single scrap loss is as high as more than 1 million
The company's challenges are: how to effectively reduce the cost caused by quality defects; how to help ordinary engineers who do not have a statistical background to analyze and solve quality problems using statistical methods; if the assembly accuracy of photovoltaic products is improved to ensure the photoelectric conversion rate, etc. The stability of key quality indicators reduces the losses caused by rework and scrap.
Solution: QuAInS system's data acquisition module, quality monitoring and reporting module, customized quality analysis and improvement functions; centralized implementation of the system; professional training and service of quality analysis methods;
results: the system runs smoothly and effectively prevents defects, rework and recall Play an important role in analysis; analysis templates and reports allow more engineers to participate in the analysis and improvement of actual problems. Monthly scrap costs have dropped by an average of 32.1%.
Case 4: A large computer and mobile phone component manufacturer
Challenge: The company is a well-known domestic computer and mobile phone component manufacturing company with a large scale and nearly 8,000 employees in a single factory. The company produces a variety of products with both high precision requirements (more than four decimal places) Machining parts, there are various connectors, coils, small PCB and other electronic products.
The company's main challenges include:
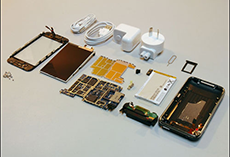
1. Large amount of data: the company has more than 1,600 CNC machining machines, plus other production equipment and diversified products. The average monthly measurement data volume is as high as 15 million, and the peak month is as high as 20 million. Measurement data; system users number up to several hundred. Such a large amount of data is a huge challenge to the stability and computing performance of any system operation.
2. The company's original SPC quality monitoring system has been running for more than 5 years, but the response speed is obviously slow, and many functions can no longer meet the new requirements of customers for its quality control. The upgrade and development work of the original system supplier based on the old system also ended in failure. How to choose a supplier with reliable technical strength and strong ability to customize products has become one of the main challenges
3. There are many customers in the company. Each customer requires the delivery of quality reports with different contents and formats. The company has to arrange a special team to produce various quality reports.
4. The company's production workshops are located in two different places, and the data volume is relatively large, but we want to use the same server and database
solution: data acquisition module, quality monitoring and reporting module, analysis and report automation and customization of QuAInS system Development services; Centralized implementation of the system (servers are located in one factory area, and other factory areas ensure user experience through special data processing); Professional training and services in quality analysis methods;
Results: The system runs smoothly and plays an important role in effectively preventing defects, rework, and recall Function; The system operation method is customized to be similar to the original old system as much as possible to shorten the learning cycle of employees and reduce the difficulty of use; it meets the requirements of customers for quality control systems and processes during quality audits; the time for data collection and quality report production is greatly reduced .
Case 5: An auto parts company achieves efficient data concentration and quality control
Challenge: The company is a domestic enterprise specializing in the production of small and medium-sized vehicle engines and parts, with an annual output of 200,000 sets of various models
The company's main challenges include:
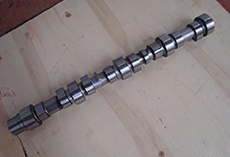
The company's quality headquarters is responsible for coordinating and managing the quality control and continuous improvement of the factories in two different locations. The production lines and measurement workshops of the two factories have a large number of data measured with three-dimensional coordinate measuring machines (CMMs), roundness meters, image measuring instruments, etc., but these data are scattered and stored in independent data files with different formats. Again, this poses a number of challenges for the use of this data:
1. Often the roundness measurement data file of the same part is on one computer, and the length or other size measurement data file is on another computer. Every time you perform data analysis, you need to first collect the data from various places. It takes a lot of time to sort out before analyzing
2. It often takes a long time from the generation of measurement data to the formation of quality data analysis results. It is not possible to understand the quality status of the process in time to prevent the occurrence of substandard products.
3. The management staff of Quality Headquarters need to urge many times each time to get the data and analysis results provided by each factory, unable to understand the quality status of each factory in real time.
Solution: data acquisition and management system, quality monitoring and early warning system. The former helps to upload the measurement data to the central database in real time and centrally stores them in accordance with the format and logic set by the implementation, eliminating data silos; the latter helps prevent the occurrence of non-conforming products, and the quality control dashboard is provided to help the management staff of the quality headquarters The office can understand the status of each production machine in each factory, and can check the progress of the quality alarms by relevant personnel at any time.
Achievements: Eliminated data silos and made the use of measurement data a breeze; early quality warnings significantly reduced the number of shutdowns and significantly reduced the scrap rate of products; managers were more transparent about the quality control of each factory Instant and effective.
You are welcome to contact us for more success stories about QuAInS.